Jaw Crusher VS Cone Crusher: 9 Key Differences
Crusher is very important equipment in the mining machinery industry, because many minerals need to be crushed before subsequent processing, and the crushing process in place can lay a good foundation for subsequent production.
If you want to complete the crushing work quickly, proper crusher is needed. Commonly used crushing equipment includes jaw crusher, cone crusher, impact crusher, vertical shaft impact crusher, hammer crusher, etc., they can process different materials with different requirements.
Among these crushers, jaw crusher and cone crusher have similar crushing principle, but different in many ways.
Lets’ talk about the differences between jaw crusher and cone crusher.
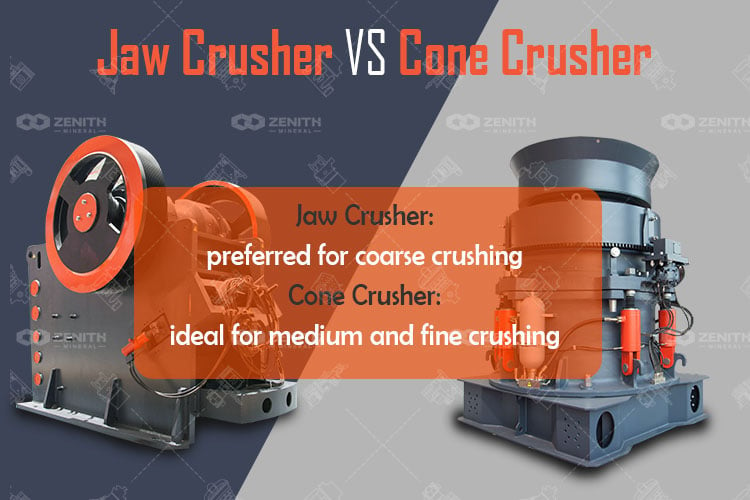
Jaw crusher: preferred for coarse crushing
Jaw crusher has the advantages of simple structure, high reliability of continuous operation and low price. Its ore outlet is adjustable, and the height difference of plant required for equipment layout is small.
The jaw crusher has large crushing ratio, which means that jaw crusher can crush large materials over 1000mm into particles smaller than 100mm. In crushing and sand production plant, jaw crusher is the preferred equipment for coarse crushing of materials with compressive strength not exceeding 320 MPa.
So, if you want to process rocks with large particle size, jaw crusher is the better choice.
Cone crusher: ideal for medium and fine crushing with good cubical shape
Cone crusher is a kind of crushing machine for raw materials in metallurgy, construction, road building, chemical and silicate industries. According to the different crushing principles and product particle sizes, it can be divided into many models. Cone crushers are widely used in mining, smelting, building materials, highways, railways, water conservancy and chemical industries. The cone crusher has large crushing ratio, high efficiency, low energy consumption, uniform product size, and is suitable for medium and fine crushing of various ores and rocks.
When the raw materials are small and the hardness is high, cone crusher is recommended. And with the adoption of lamination crushing principle, cone crusher has good cubical shape of the final products.
Jaw crusher VS cone crusher: 9 main differences
Many customers do not know the differences between jaw crusher and cone crusher. In order to help you to know them better and to know how to choose jaw crusher vs cone crusher, here are the 9 main differences between jaw crusher and cone crusher:
1. Different in working principles
The working mode of jaw crusher is curved extrusion type, and materials are crushed in the crushing chamber composed of movable jaw and fixed jaw.
The cone crusher adopts laminated crushing principle, and the mantle continuously moves towards concave to extrude the materials sandwiched between them to crush them.
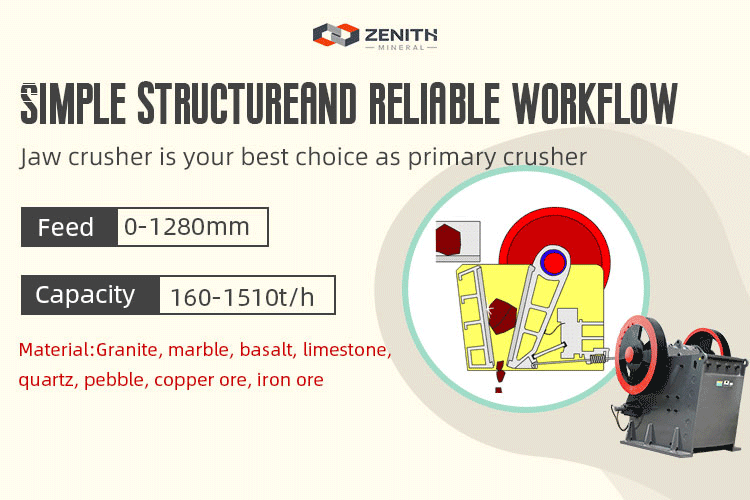
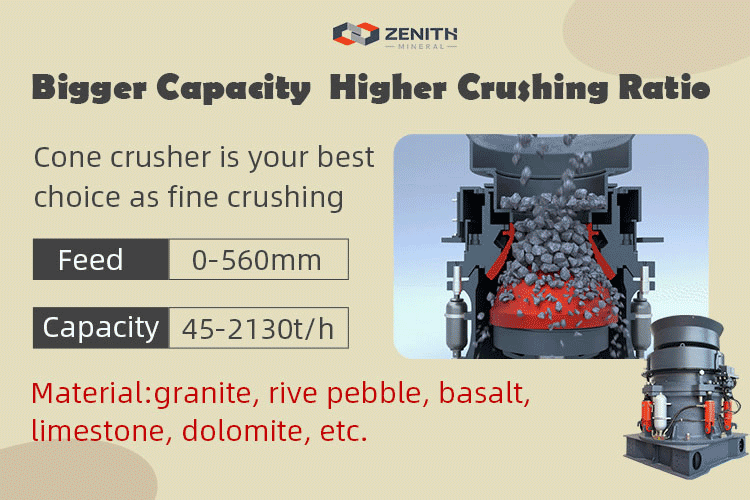
2. Different in production characteristics
Generally, jaw crusher and cone crusher has the following production characteristics:
Feeding size: The feeding size of jaw crusher is relatively large, and it can generally handle materials below 1200mm, which the feeding size of cone crusher is relatively small, generally below 560mm.
Production capacity: cone crusher has larger production capacity than jaw crusher. The largest production capacity of cone crusher can reach to 2130t/h while the largest production capacity of jaw crusher is about 1500t/h.
Compressive strength: jaw crusher and cone crusher both can process raw materials with compressive strength within 300-350Mpa.
Tips: the specific data is based on our models of jaw crusher and cone crushers.
3. Different in materials
Jaw crusher is suitable for a variety of materials with different hardness, such as pebbles, granite, limestone, barite, etc.
Cone crusher is more suitable for materials with higher hardness, such as granite, rive pebble, basalt etc.
4. Different in positions in crushing plants
Jaw crusher has large feed opening, which is suitable for primary crushing, also known as coarse crushing;
Compared with jaw crusher, cone crusher has smaller feed opening, which is often used for secondary or tertiary crushing of materials;
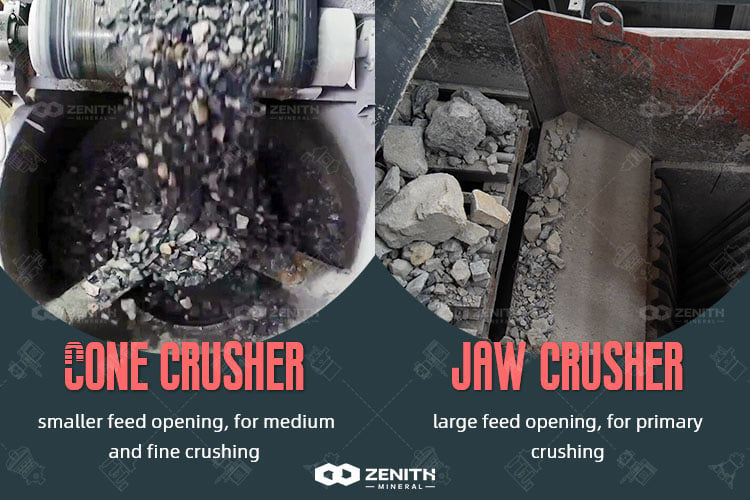
5. Different in scopes of application
There are many types of jaw crushers, which can be used in large, medium and small-scaled sand and gravel production plants; cone crusher is more suitable for large and medium-sized sand and gravel production plants.
6. Different in sizes and structures
In terms of volume, jaw crusher is smaller than cone crusher. From the perspective of the overall structure, the cone crusher is 1.7-2 times heavier and 2-3 times higher than the jaw crusher with the same feeding opening size. So, it needs more money to build the factory of cone crusher.
7. Different in grain shape
Due to the crushing principle, cone crusher has better grain shape than jaw crusher. Generally, you need shaping equipment after jaw crusher for better grain shape.
And cone crusher can be used for shaping because of the adoption of lamination crushing principle, which makes the final products have good cubical shape.
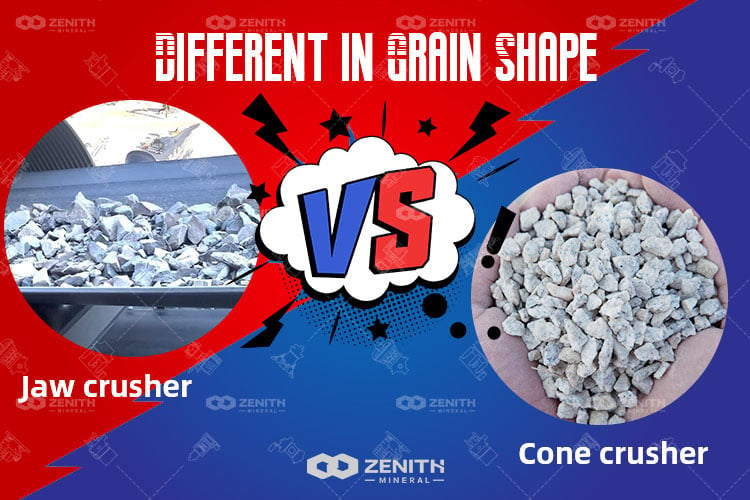
8. Different in prices
Due the structures and features, cone crusher is much more expensive than jaw crusher.
9. Different in maintenance costs
In the production process of crushers, regular maintenance is necessary. Although the investment cost of cone crusher is high in the early stage, the failure rate is low in the production process, and the replacement cycle of wearing parts is long, and the maintenance and overhaul is convenient, which saves a lot of manpower and material resources.
Jaw crusher VS cone crusher, how to choose?
After the comparison, we know the 9 differences between jaw crusher and cone crusher. While choosing crusher, you need to consider the following factors:
Firstly, consider the investment cost. When jaw crusher and cone crusher both can meet the production requirements, you can choose jaw crusher, which is cheaper;
Secondly, for large-scaled production line, cone crusher is the better choice;
Thirdly, when crushing wet cohesive ore, it is better to choose jaw crusher; when crushing flaky or long strip hard ores, cone crusher is recommended.
But if you are not sure which one is suitable for you, contact Zenith engineers for more information. We will recommend suitable jaw crusher and cone crusher for you according to the specific situation and production requirements.